In recent years, several tools and methods have become available to fluid power engineers to improve performance and reduce energy consumption in hydraulic systems. Among these, variable speed pumps and low viscosity hydraulic fluids are two of the main drivers of energy efficiency – with benefits for both sustainability and operational costs. In this article, we explain how these two technologies are meeting the dual demands of operational efficiency and environmental compliance.

Variable Speed Pumps And Energy Efficiency
So, what is the deal with variable speed pumps, and how do they improve energy efficiency? The difference comes from their ability to respond to system demand. The fixed speed pumps traditionally used in hydraulic systems operate at a constant speed, with the same energy expenditure and power output regardless of demand. This invariably leads to energy loss and unnecessary waste, especially during low-load periods. Variable speed pumps overcome this limitation by allowing the pump to adjust its speed to dynamically match your system requirements. Benefits of this include:
- Energy optimisation: variable speed systems modulate the motor speed to supply only the hydraulic power needed at the time, which measurably reduce energy consumption, especially in systems with fluctuating loads.
- Reduced waste heat: by operating at lower speeds during partial-load cycles, variable speed pumps produce less heat, which reduces the need for cooling mechanisms and extends your component life.
- Improved system control: variable speed pumps give you better precision and control over the hydraulic application, allowing you to optimise its performance in real time.
For these reasons, variable speed pumps are now being widely adopted in manufacturing, material handling, and heavy equipment applications. An American industrial chiller manufacturer claims to have achieved around 50% energy savings by implementing variable speed pumps. This comes from a 25% reduction in flow which results, theoretically, in a 58% reduction in energy use. However, in practice, about 50% is achievable before the system pressure drops too low to maintain an adequate flow.
Low Viscosity Hydraulic Fluids
Hydraulic fluids play a critical role in bridging the energy transfer and lubrication functions in fluid power systems. Traditionally, high viscosity fluids were used, and while still effective in many applications, they often generate greater internal friction and waste more energy than lower viscosity fluids. Many applications now make use of the better flow characteristics of low-viscosity hydraulic fluids to strengthen overall system efficiency. Why you should make the switch:
- Minimise pressure drops: low viscosity fluids deliver a smooth flow of fluid through your pipelines, reducing pressure fluctuations and losses, which boosts overall operational efficiency and reduces energy consumption.
- Lower pump power requirement: with less internal friction to deal with, your hydraulic pumps need to expend less energy to circulate the fluid throughout the system, reducing energy demand.
- Greater sustainability: low viscosity fluids also have a role to play in compliance with stringent environmental regulations, as some formulations are now biodegradable – making them a more eco-conscious choice for an industry transitioning towards more sustainable practices.
Find Out More
The combined use of variable speed pumps and low viscosity fluids can reduce energy consumption in many hydraulic applications. To find out more about maximising performance while minimising energy waste, please contact HydraStar today by calling 01353 721704.
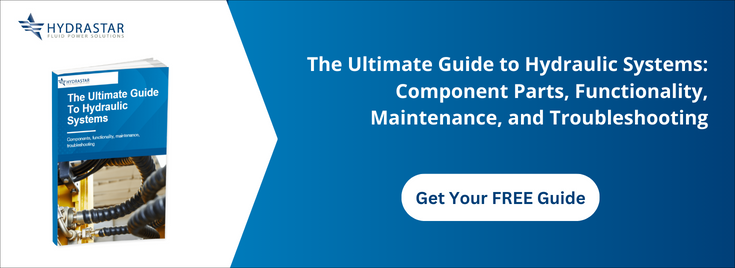