Safety and efficiency are the two golden rules of industrial fluid power system design. Hose clips and clamps are the key to achieving both, and are critical for avoiding safety issues like leaks, bursts, and equipment damage. This article provides a concise overview of all you need to know about these essential safety components, so read on to find out more.
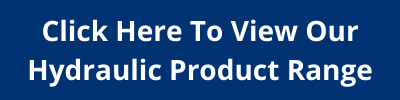
What Is The Purpose Of Hydraulic Hose Clips And Clamps?
The purpose of hose clips and clamps is to secure hydraulic hoses to their fittings, creating a tight connection that can withstand the rigours of high-pressure operations. The goal is to stop the hose from moving around when subject to pressure surges, vibrations, and external forces, as this can make the hose come loose from its fittings. Clips and clamps stabilise the hose, minimising movement that could lead to damage or material fatigue. This enhances safety because a loose or disconnected hydraulic hose can leak under pressure, and can also suddenly discharge pressurised fluid, creating a safety hazard for workers and equipment.
Specifying the incorrect components or misapplication can lead to hose failure or even catastrophic fluid leaks, so it’s important to install the correct component for your application.
What size do you need? Let’s start by determining the size of clamp you need, which needs to be accurate for the component to provide optimum safety. Use callipers or a diameter gauge to measure your outer hose diameter (OD) under operating load to select the correct clamp size. Please check your manufacturer’s guidelines for precise sizing recommendations.
Materials: There are various materials available for different applications and purposes. For example, grade 304 and 316 stainless steel clamps are ideal for high moisture and corrosive environments (e.g. offshore and marine applications). Zinc-plated steel clips and clamps are good for moderate to austere operating environments, while nylon or polypropylene clamps are a cheap and lightweight solution for low-pressure systems, but don’t always hold up under high temperatures and heavy loads.
Installation Best Practices:
For consistent tightening, we recommend using torque-control tools rather than manual tightening. This reduces the risk of over tightening, which can damage the hose. For PEX (cross-linked polyethylene) hoses and tubes, use crimping or ear clamp tools to ensure uniform pressure distribution.
When placing the clamp, position it at least one hose diameter away from the fitting edge to avoid kinks or bulging. Some high pressure and safety- critical systems may require dual clamps – spaced apart – to provide redundant sealing.
Troubleshooting Common Issues:
“My clamps are coming loose due to vibration”
Apply a thread lock compound to the clamp screws to avoid loosening, or use self-locking or double clamps. If the system is vibrating outside of its usual parameters, this could indicate an issue with another component.
“My hose is damaged near the clamp connection”
This is usually due to the clamp having an abrasive surface or rough edge. Remove the damaged sections of hose, then replace any rough-edged clamps with smooth banded or lined clamps to avoid further damage.
“The hose still leaks even with clamped connections”
The clamp may not be attached properly, so verify fitting and also that the clamp size is compatible with your hose OD. Uneven surfaces may need gaskets or a sealing tape to provide a perfect interface between hose and clamp.
Find Out More
Get in touch with Hydrastar today to find out more about hydraulic system safety and the right choice of clips and clamps for your application.
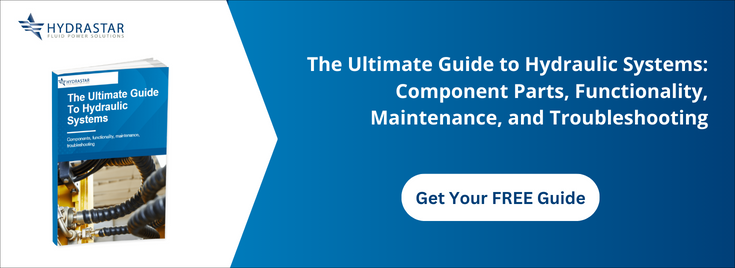
Image Source: Canva