The integration of digital technologies such as AI, virtual prototyping, and data analytics into the design process has revolutionised the way that fluid power components are produced. From pumps with the capability to adapt their flow rates according to real-time demand, to ‘maintenance free’ valves that utilise past performance data to pinpoint failure risks and minimise wear and tear, fluid power components are becoming cheaper, more reliable, and more powerful with each passing year.
How Digital Modelling Has Advanced
Over the past few years, digital modelling and simulation technologies have transformed the way that fluid power components are conceived, designed, and tested. Design engineers can now create sophisticated virtual prototypes and conduct simulation scenarios under various conditions, so that their final components meet more stringent performance, sustainability, and reliability standards. This has progressively reduced the need for expensive physical prototypes, reducing development timelines and costs.
In high-performance valves, for example, digital modelling allows engineers to simulate the fluid dynamics within the valve, predicting how different designs will impact flow characteristics and pressure drops, and optimising the valve for specific outcomes.
Benefits Of Innovative Component Design
For end users. OEMs, and engineers alike, the adoption of digital technologies in component design provides several benefits. Firstly, for example, it has improved the energy efficiency of many pumps, valves, motors and other components, significantly reducing energy consumption. By optimising components to operate more efficiently – even if the design remains visibly unchanged – applications cost less to operate and have a lower environmental impact.
Digital design technologies can also increase the reliability and durability of fluid power components. Predictive analytics and modelling, for instance, can identify potential failure points and address these at the design phase, producing components that are more robust and less prone to downtime. This reduces the lifetime cost of maintenance and repair and can extend the lifespan of components compared to previous iterations.
What Does The Future Hold?
Looking ahead to 2025 and the remainder of the decade, it looks as if the fluid power sector is poised for further innovation driven by digital technologies. The widespread adoption of AI-augmented design tools, for example, will accelerate the development of next-generation fluid power systems by enabling engineers to automate complex calculations and design simulations to arrive at the best solution in a fraction of the time.
Advanced digital twins are another important innovation in component design. These virtual replicas of physical components give engineers a full life-cycle view of a component at the design stage, enabling a more proactive approach to maintenance, monitoring, analysis, and system optimisation. So-called smart components are another exciting area of development that design engineers should look out for. Smart components are equipped with various sensors and connectivity features that allow them to self-adjust to changing operational conditions, with easier integration with other components and IOT (Internet of Things) applications.
Next Steps
Digital technologies are fundamentally reshaping not only fluid power applications, but also the design and capabilities of individual fluid power components. To find out about the latest innovations and to achieve the best solution for your application and project goals, please contact HydraStar today by clicking here.
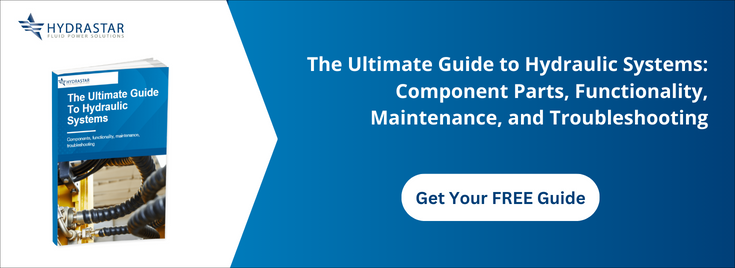
Image Source: Canva