Industry 4.0 is one of the most commonly used (and misused) catchphrases in the manufacturing and industrial sectors today. Originating as the name of a digitalisation initiative sponsored by the German government in 2011, industry 4.0 has subsequently spread internationally as a catchall phrase to describe the convergence of the physical and digital worlds by infusing digital automation and data management systems into manufacturing.
Fast forward to 2024, and the ‘Fourth Industrial Revolution’ is set to transform the fluid power sector in more ways than could have been imagined a decade ago, opening the door to smarter systems that prioritise performance while expressing unprecedented levels of efficiency and adaptability.
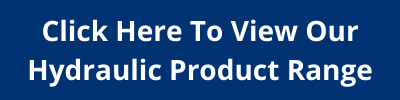
Key Components Of Industry 4.0 For Fluid Power Engineers
So, what makes an application ‘industry 4.0 compatible?’ Incorporating the following elements into your fluid power designs – or at least the potential to incorporate them at a later date – is the key to maintaining compatibility with industry 4.0 systems and applications.
1) The Internet of Things (IOT): the Internet of things is essentially a network of sensors that relay operational data from a fluid power application to a monitoring and control system, and transfer operating controls back to the application remotely. By embedding sensors into your designs and enabling IOT connectivity, hydraulic systems can transmit operational data to a centralised control system for better monitoring and analysis. There are wide-ranging benefits to this, including early fault detection, real-time performance optimisation, and proactive maintenance.
2) Predictive maintenance: predictive analytics enables engineers to forecast potential system failures and allows proactive maintenance and replacements of worn parts, thereby reducing system downtime and extending the life cycle of the application.
3) Adaptive controls: Industry 4.0 fluid power applications must evolve to integrate intelligent controls that can autonomously adjust operational parameters in response to real-time feedback, helping sustain peak performance. This will help operators reduce fuel and energy waste and improve the sustainability of their applications.
4) Energy efficiency: advanced energy saving mechanisms, such as variable speed drives, can be used to create efficient systems that contribute to leaner and more sustainable manufacturing processes.
5) Data security: a continual flow of data across Internet networks is the bedrock of Industry 4.0, so protecting the gathered and transmitted data within your applications from cyber threats and network faults is crucial to maintaining the integrity and reliability of the entire operation.
Like other trends, ‘Industry 4.0’ is more an ‘eat what you like buffet’ than a ‘set menu’. While it’s useful to be aware of what technologies are available to support the efficiency and performance of your applications, not all briefs will require full adoption of Industry 4.0 technologies.
What Are The Advantages Of Future Proofing?
Not all fluid power engineers are signed up Industry 4.0 enthusiasts, with the belief that the new components and failsafes add an unnecessary and unwanted level of complexity to hydraulic and pneumatic designs. However, future proofing your fluid power systems for Industry 4.0 could bring a range of benefits, including superior machine output, better precision and control, heightened productivity, reduced downtime, and lower operating costs.
Next Steps
With a large range of advanced fluid power components continually in stock, and partnerships with the world’s leading manufacturers, Hydrastar can help you stay abreast of technological advancements and equip your project with the agility to respond to changing market demands. To find out more, please contact one of our fluid power specialists today by 01353 721704.