Two of the most common causes of damage and premature failure in hydraulic cylinders are side load and misalignment. These issues can cause significant wear and tear to your cylinders over time, often necessitating early replacement or repair, and sometimes leading to critical system failure. In this article, we’ll look at the main causes of side load and misalignment issues in hydraulic cylinders, their effects on operation, and practical tips on how to prevent them in order to minimise wear and tear.
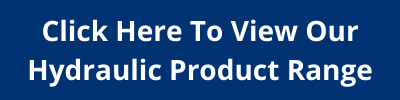
What Is Side Loading?
Side loading occurs when a force is applied to the rod of a hydraulic cylinder in a direction other than its intended range of motion. This force can come from various sources, such as incorrect mounting, an unbalanced load, excessive vibration, or external factors like a collision or sudden impact.
One of the main causes of side load is inadequate alignment between the cylinder and the load it is supporting. In other words, when a cylinder is not aligned correctly, it creates an imbalance that puts additional stress on one side of the cylinder, causing it to bear more load than the other. Over time, this can lead to uneven wear and component fatigue, with a heightened risk of premature failure.
Sideloading can also arise due to poor mounting techniques, such as using incorrect hardware, or misaligned pivot points – these human errors create excessive strain on the cylinder under load, leading to performance issues and potential damage.
Common Misalignment Issues
Misalignment can occur in both the hydraulic cylinder and its mounting components, causing the piston rod to move about unevenly. There are various ways this can come about, including manufacturing defects, misaligned machinery, or errors during installation. Whatever the cause, if a cylinder is not correctly aligned, it can cause excessive wear on its seals and bearings. As a result, the cylinder may leak hydraulic fluid – losing efficiency and potentially causing pollution. Misalignment also leads to uneven force distribution throughout the system, making the cylinder less powerful and putting additional strain on surrounding components. Damage breeds further damage.
What Can Be Done?
The key to preventing sideloading and misalignment issues in your hydraulic cylinders is to ensure the correct alignment between the cylinder and its mounting point. There are several ways you can do this:
1. Use Precision Cylinder Mounting Techniques:
Use precision tools and processes to ensure that each cylinder is installed straight and parallel to its intended motion, to avoid side load.
2. Check Load Balances:
Before operating the cylinder, check that the load is evenly distributed on both sides – this will prevent one side from bearing more weight than the other and further reduce the risk of side loading.
3. Use High-quality Mounting Hardware:
Low quality or defective mounting hardware can cause cylinder misalignment. Invest in high quality components that are suited to your specific application – get in touch with one of our specialists if you’re unsure.
4. Regularly Inspect And Maintain Your Hydraulic Cylinders:
Routine and proactive maintenance checks can help identify the early signs of side load and misalignment issues (i.e. uneven wear), allowing early resolution to avoid expensive damage.
Find Out More
Like all mechanical components, even the best hydraulic cylinders are prone to wear and tear with repeated use. However, by being aware of side load and misalignment and the damage they can cause, you can hopefully reduce your unscheduled downtime, lifetime repair costs, and any unexpected loss in efficiency. To find out more, please contact one of our experienced team today by clicking here.
Image Source: Canva