How does a hydraulic system work?
What components are used in a hydraulic system?
What are the advantages of hydraulic systems?
What are the disadvantages of hydraulic systems?
Hydraulic systems are a type of fluid power system that uses pressurised liquid to transmit force. A highly versatile and powerful tool, they are commonly used in a variety of applications in most fields of industry, including manufacturing, automotive, medical devices, and defence.
While it is often recognised that hydraulics facilitate the movement of large or heavy items, such as construction materials, they can also be used to apply extremely precise and controlled force to achieve accurate results.
In this guide, we’ll explain everything you need to know about hydraulic systems, including how they work, how they are used in different industries, their common components, and their advantages.
How does a hydraulic system work?
A hydraulic system utilises the fundamental properties of fluids to transmit force and power, and to control mechanical movements.
At its core, it operates on the principle of Pascal’s Law, which was devised by French mathematician and physicist Blaise Pascal in the mid-17th century.
Pascal’s law states that when pressure is exerted on a confined fluid, there is an equal increase in pressure at every other point in the container: in other words, through the liquid to the walls of the container, with no loss of pressure.
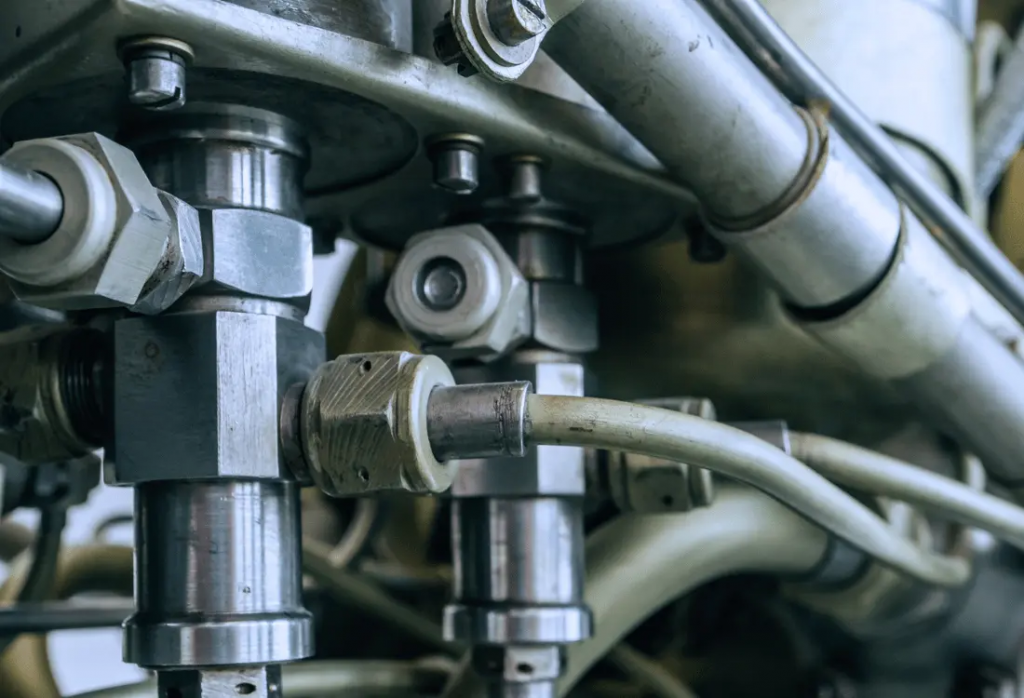
For example, if pressure is applied to one end of a closed container of liquid, the same pressure will be applied to the opposite side. It is this principle of physics that enables force to be multiplied through a liquid to affect a larger or heavier object.
A hydraulic system comprises several key components:
- A fluid, usually oil
- Valves
- A Reservoir
- Actuators, such as cylinders or motors
- A pump
- Piping
When a force is applied to the fluid by the pump, it becomes pressurised and is directed through a network of pipes and valves to reach the desired location.
In the case of a simple hydraulic cylinder, the pressurised fluid enters one side of the cylinder, causing a piston to move. As Pascal’s Law states, if a small amount of force is applied to the piston at one end of the cylinder, the identical force will be applied to a larger piston on the opposite side. Therefore, a small amount of force can be used to control a much larger force which can be used for lifting, pushing, or any number of mechanical tasks.
The most significant benefit of hydraulic systems lies in their ability to transmit force and power over significant distances while maintaining consistent pressure. Because the fluid is incompressible, the force applied at one end is almost instantaneously transmitted to the opposite end. This makes hydraulic systems incredibly efficient for a range of applications, from heavy machinery in construction to braking systems in cars.
By controlling the flow of the hydraulic fluid using valves, operators can precisely regulate the movement of actuators. Additionally, hydraulic systems can be designed with multiple actuators connected to the same fluid source, to enable complex and synchronised movements. The versatility and power of hydraulic systems make them essential in industries in which high force output, precision control, and reliable operation are vital.
What are the common applications of hydraulic systems?
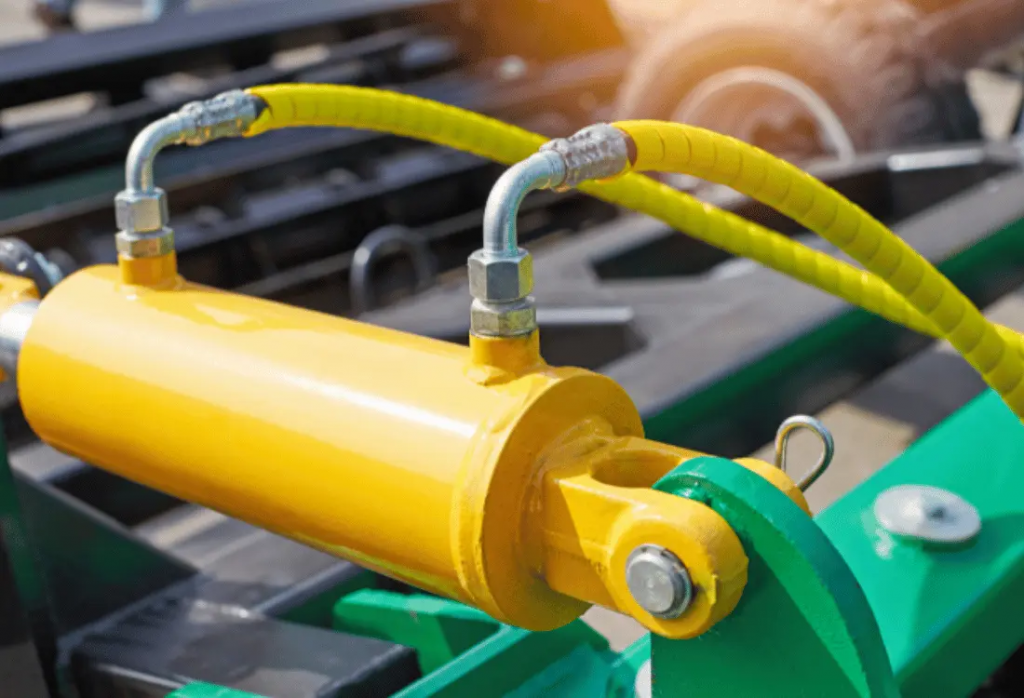
Hydraulic systems are a versatile and powerful technology that are used in a variety of applications, including construction equipment, industrial machinery, cars, aircraft, and medical devices, among others. A vital part of modern industry, hydraulic systems will continue to be used in a variety of new and innovative ways in future.
Some common uses of hydraulic systems include:
Construction equipment:
Hydraulic systems are a feature of a range of construction equipment, including excavators, bulldozers, cranes, and diggers. Hydraulics make possible tasks which would otherwise by time-consuming and laboursome to complete manually, such as the lifting of heavy objects and the excavation of soil and concrete.
Industrial machinery:
Many manufacturing businesses depend on hydraulic systems for production and processing equipment, such as robotic arms, heavy printing and pressing machines, forklifts, and die casters. Hydraulics are essential for processes that move materials, cut metals, and perform other tasks that require a lot of force.
Automotive:
In the automotive industry, numerous components in vehicles rely on effective hydraulic systems, most notably brakes and power steering – actions that require a high degree of force to deliver a rapid response, thereby protecting the occupants of the vehicle and other road users.
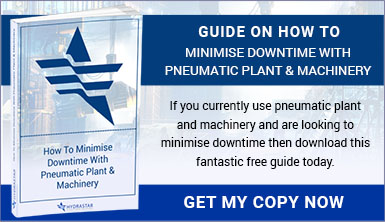
Aircraft:
Hydraulic systems play a key role on-board aircraft, particularly to power moving parts such as the landing gear, ailerons, elevators, flaps, and rudders. The force required to manoeuvre large and aerodynamically sensitive surfaces is beyond what manual control could achieve, whereas hydraulic actuators provide the necessary power and responsiveness to pilot inputs to ensure a safe and controlled flight.
Medical devices:
Hydraulic systems are integral in the medical field for applications such as patient lifts and adjustable hospital beds. These systems utilise pressurised fluids to enable smooth and controlled movements to enhance patient comfort and reduce the risk of injury to healthcare staff. Advances in medical science are also unveiling new ways for hydraulics to be used, for example, in advanced prosthetic limbs to replicate natural, fluid movement and enhance functionality for amputees.
Other applications:
Due to their exceptional versatility, hydraulic systems are used in many other applications, from marine equipment and theme park rides to robotics and missile deployment systems.
Welcome to The Ultimate Guide To Hydraulic Systems
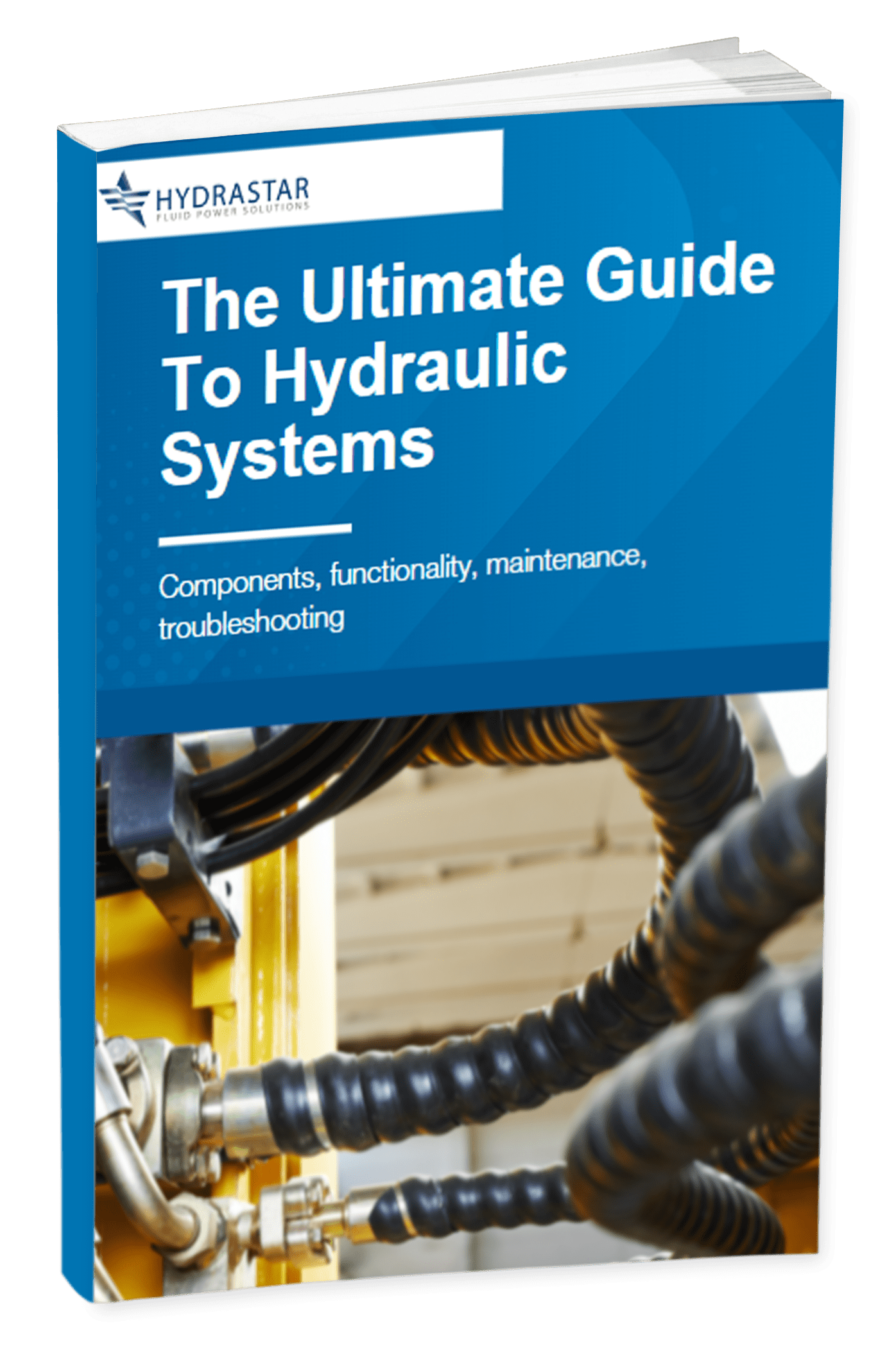
In this guide, you will:
- Uncover the essential elements of hydraulic systems, from pumps and cylinders to valves and actuators.
- Explore the seamless integration of components, realising how they contribute to precise control, high power density, and overall system efficiency.
- Gain valuable skills in identifying, diagnosing, and addressing common issues.
Simply fill out the form to the right to get your FREE copy!
What components are used in a hydraulic system?
The specific components in a hydraulic system will vary depending on the application; however, broadly speaking, the following components are to be commonly found in most types of system, which we can supply at Hydrastar:
Pump:
The hydraulic oil pump is used to move the fluid through the system, from the valve to the cylinder. It is powered by an electric motor, an internal combustion engine, or another source of power, such as compressed air. The efficiency of the pump is measured in gallons per minute or pounds per square inch (psi).
Reservoir:
The reservoir stores the excess hydraulic fluid and acts as a buffer to prevent the pump from running dry. Because heat is generated from fiction in a hydraulic system, the reservoir allows it to dissipate through the metal walls and also allows trapped air to escape to improve the efficiency of the system.
Hydraulic fluid:
Most hydraulic fluids are vegetable, petroleum, or mineral-based oils, which are chosen for the desired application and the specification of the fluid. Oil is used in hydraulic system for several reasons: it is highly efficient in transmitting power from the pump to the actuators; it lubricates moving parts, preventing them from wearing prematurely; it can seal minor leaks in the system to prevent loss of pressure; it absorbs heat from moving components and prevents overheating; and it removes contaminants which can damage the sensitive system components and reduce efficiency.
Valves:
Valves are used to control the flow of hydraulic fluid in the system by directing flow, regulating pressure, or preventing backflow. The proper functioning of valves ensures safe and accurate operation within the hydraulic system, so it is vital to choose valves from a reputable manufacturer, such as Webtec and Atos who are electrohydraulic specialists.
Cylinders:
Cylinders, which are used to convert hydraulic fluid power into mechanical force, have a piston that moves back and forth within the cylinder chamber. When pressurised hydraulic fluid is applied to one side of the piston, it moves the piston in that direction.
Filters:
Filters are responsible for maintaining the cleanliness of the hydraulic fluid. By removing contaminants from the fluid, they prevent the system from becoming clogged which, otherwise, would cause damage to sensitive components. We supply filters from established manufacturers, including MP Filtri.
Hoses:
At Hydrastar, we recommend Gates hoses which are used in both low-pressure and ultra-high-pressure assemblies. Hoses, through which hot fluid will move between different components of the hydraulic system, must be strong enough to withstand the extremely high pressure and flexible enough to allow for movement of the components.
Couplings:
Couplings connect the hoses with other components in the hydraulic system and must be able to withstand high pressure to prevent the hoses from becoming detached, while facilitating quick and easy connections and disconnections. Couplings may also offer features such as valving mechanisms to control fluid flow and prevent accidental disconnections. At Hydrastar, we stock an extensive range of couplings for low-pressure and high-pressure hydraulic systems, from trusted manufacturers, including Gates and Holmbury.
What are the advantages of hydraulic systems?
Hydraulic systems are an indispensable technology in a wide spectrum of industries, offering many advantages that enhance efficiency, productivity, and quality standards.
Power density
A primary advantage of hydraulic systems is their exceptional power density. Capable of delivering high levels of force relative to their size, hydraulic systems are well-suited for applications where compactness and strength are required. Power density is particularly evident in heavy machinery, where hydraulic systems effortlessly lift, move, and manipulate massive loads with relative ease.
Exceptional control
Hydraulic systems offer unparalleled precision in control, with the ability to modulate force with pinpoint accuracy to support delicate tasks as diverse as using surgical instruments in healthcare to cutting intricate components in manufacturing. By achieving exceptional levels of precision, organisations can achieve enhanced product quality, reduced waste, and excellent safety.
Force amplification
In some scenarios, it’s necessary for a small input force to generate a large output force, such as in braking systems in vehicles or in industrial presses. Hydraulic systems are highly regarded for their ability to amplify force, allowing for the multiplication of input energy.
Adaptability
Hydraulic systems can be designed to meet a variety of requirements, from the delicate and precise needs of medical equipment to the robust demands of construction machinery. They can also operate in hostile environments as well, such as in wet weather, extreme temperatures, and even underwater.
Reliability
Because hydraulic systems have few moving parts, wear and tear is minimal, so long-term costs are low and extended periods of disruptive downtime are unlikely. Hydraulic oil is selected carefully for each application, and is highly effective in removing contaminants that could cause damage to sensitive components, lubricating moving parts to prevent wear, and absorbing heat to prevent technical problems from occurring.
Shock absorption
Finally, hydraulic systems exhibit excellent shock-absorption properties due to the incompressible nature of fluids, which provides a cushioning effect that protects delicate components from sudden jolts and impacts. Consequently, machinery and equipment are more likely to offer longer, reliable service, particularly on challenging terrain such as construction sites.

What are the disadvantages of hydraulic systems?
While hydraulic systems offer numerous advantages, they are not without their drawbacks, so it’s wise to be informed about the disadvantages to ensure you make a worthwhile investment for your business.
Fluid leakage
Finally, hydraulic systems exhibit excellent shock-absorption properties due to the incompressible nature of fluids, which provides a cushioning effect that protects delicate components from sudden jolts and impacts. Consequently, machinery and equipment are more likely to offer longer, reliable service, particularly on challenging terrain such as construction sites.
However, you can reduce the likelihood of a leak by investing in high-quality components from reputable manufacturers, such as Gates, Holmbury, Atos and Webtec whose parts we stock at Hydrastar. Also, it’s essential to consult our experts when purchasing components, as we can advise on their suitability for the intended application. We also offer a full expert design service and on-site maintenance to keep your hydraulic systems in optimum condition.
Regular maintenance
Hydraulic systems demand meticulous upkeep to ensure optimal performance, including monitoring fluid levels, checking for leaks, and replacing worn-out components. Failure to adhere to a strict maintenance schedule can lead to unexpected downtime and increased operational costs, so it’s important that you budget for regular maintenance. At Hydrastar, we stock an extensive range of Diagnostic and Test equipment for hydraulic systems, from trusted manufacturers, including Webtec.
At Hydrastar, our engineers are available for on-site technical call outs in which we will carry out detailed fault finding to identify and isolate potential issues before they become serious problems, thereby helping you to keep your hydraulic system in full working order.
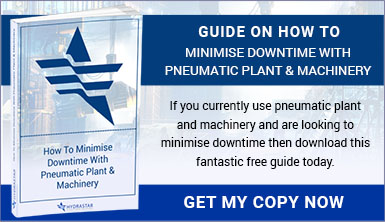
Energy efficiency
Hydraulic systems are generally less energy-efficient compared to alternative technologies due to the constant circulation and pressurisation of fluid, which results in energy losses through friction and heat generation.
Improving energy efficiency requires a combination of innovative design, proper maintenance, and the integration of new technologies. At Hydrastar, we can provide expert technical advice about how to enhance the energy efficiency of your hydraulic system, by:
- Selecting high-efficiency components such as pumps, motors, and valves, that are designed for optimal energy usage.
- Ensuring proper sizing to ensure that hydraulic components are properly sized for the intended application.
- Implementing Variable Speed Drives (VSDs) which adjust the speed of components based on the actual load requirements.
- Employing load-sensing hydraulic systems that adjust the flow rate based on the load demand.
- Choosing hydraulic fluids with low viscosity and high thermal stability to reduce friction losses and heat generation.
- Integrating smart control systems to optimise the operation of hydraulic components, such as closed-loop feedback controls to maintain precise pressure and flow levels and reduce waste.
- Regularly inspecting hydraulic systems for leaks and promptly repairing any identified issues
- Using hydraulic accumulators to store energy during low-demand periods and release it during high-demand periods, thereby reducing the need for constant pump operation.
- Installing heat exchangers to manage the temperature of hydraulic fluid and maintain optimal fluid temperature to energy consumption.
If you’re concerned about whether a hydraulic system is right for your business, or you wish to improve the performance of your existing system, at Hydrastar we can offer expert advice to help you to get the best from your investment. Our expert staff have years of experience designing hydraulic systems for a range of applications and industries, and can provide reliable technical advice to support your decision making.
Your next steps
At Hydrastar, we offer expert hydraulic design services, on-site maintenance
and servicing, and over 100,000 catalogue components for customers throughout the UK, with same-day despatch for in-stock products ordered
by 2.30pm. To find out more about our services, please browse our catalogue or call us on 01353 721704 for friendly and professional advice.