Water saturation in hydraulic oil is a common issue that service engineers face, and it can be difficult to detect until problems arise – by which time it could cause serious damage. In this article, we’ll look at the ‘cloudy oil problem’ caused by water saturation and what you can do to prevent it.
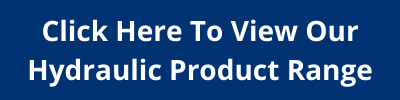
Why Is Water Saturation Such A Murky Issue?
Water and oil are not harmonious roommates at the best of times, and when it finds its way into hydraulic oil, water can result in corrosion, reduced lubrication, and a lower service life for important components. It can also instigate pressure spikes and aeration, undermining system performance and efficiency. While other types of contamination can also cause these issues, water saturation is a unique problem that is worth dealing with in its own right.
One of the visible signs of water contamination in hydraulic oil is that the oil becomes cloudy or milky in appearance, which is caused by water particles becoming trapped in the microscopic spaces between the oil molecules.
How To Prevent Water Saturation In Hydraulic Oil
Water can seep into your hydraulic oil through various means, including condensation, leakage, and direct contamination, and once it’s there, it can be tricky to remove, so what are the best ways of preventing water saturation from occurring?
- Regular servicing and maintenance: regularly maintaining your hydraulic system, including checking the system for leaks, and ensuring that all seals and gaskets are tight, is a good way of preventing contamination, or at least significantly lowering the risk. We also recommend monitoring your hydraulic oil for water content through oil analysis tests, addressing issues at an early stage before they become too severe.
- Storage conditions: hydraulic oils are vulnerable to exposure to sunlight, as strong UV rays can cause the oil to break down and create an ideal environment for water to enter. Hydraulic oil containers should, therefore, be stored in cool areas out of the way of direct sunlight, and in airtight containers to prevent contamination.
- Water-absorbing filters: many hydraulic systems employ water-absorbing filters to capture surplus water before it enters the hydraulic oil. These filters have a special hydrophilic coating that actively attracts and captures water molecules. Filters should be changed at regular intervals to maintain their efficiency.
- Dehumidifiers: installing a dehumidifier in your hydraulic system room is a good way of removing excess moisture from the air, thereby reducing the humidity level in the space and preventing condensation from entering your hydraulic oil.
Tips For Removing Water From Hydraulic Oil
If you’ve already detected the tell-tale signs of water saturation – e.g. through a test strip – there are several approaches that can be employed to resolve the problem. These include using a centrifuge to spin the oil and separate the water from the oil, or to inject water-removal additives to the oil to bond with H2O molecules to form larger droplets, which can then be filtered out from the oil more easily.
However, one of the most cost-effective and efficient methods is to use a vacuum dehydrator, which removes water from the oil by boiling it at a low temperature. During vacuum dehydration, the oil is first preheated to reduce its viscosity, before being exposed to a low pressure environment that causes dissolved water vapour and gases to separate from the oil. The oil is then further subjected to low pressure, causing the water to vaporise, after which the dehydrated oil is passed through a fine filter to remove any remaining particulate contaminants.
Vacuum dehydration is particularly effective at removing dissolved and emulsified water, which can be challenging to eliminate using alternative treatment methods.
Find Out More
For advice about hydraulic system maintenance and how to prevent contamination in your system at the design stage and throughout its lifecycle, please call one of the experts at Hydrastar on 01353 721704.
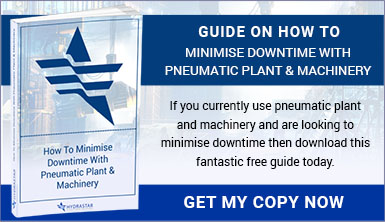