Hydraulic fluid power systems are the workhorses behind some of the most critical applications in various industries, from heavy construction equipment to manufacturing production lines. When these systems experience unscheduled downtime, therefore, the impact on output can be significant, delaying projects and driving up costs. This article will cover a selection of troubleshooting techniques and preventative practices that engineers can use to minimise the risk of disruptions and maintain operational efficiency.
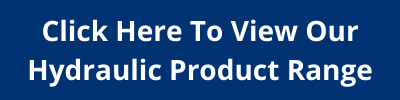
1. System anatomy
The components most prone to issues in most hydraulic systems are the pump, reservoir, valves, and filters. These are connected by hydraulic lines, which also sometimes develop problems. Familiarity with the system anatomy or architecture of your application will help you to pinpoint the exact area where downtime originates.
2. Diagnostic tools
Having access to a good diagnostic tool kit will improve the accuracy of your troubleshooting process and reduce downtime. Traditional pressure gauges and flow meters are joined by thermal imaging cameras in evaluating modern system performance. In addition, contamination monitors can help identify particulate levels in your hydraulic fluid, which can be a major factor in system inefficiency and wear.
3. Rule out common failures first
Some failures are commoner than others, such as unexpected pressure drops, hydraulic fluid leaks, and slow actuator movements. Therefore, it makes sense to troubleshoot these areas first. For example, a visual inspection along your hoses and seals is often sufficient to reveal fluid leakage points. You should also verify the system pressure against its specifications, as an incorrectly calibrated relief valve can lead to performance issues. Clogged filters are another common issue, so examine your filter elements carefully for dirt buildup. A blocked filter can restrict fluid flow rate and increase your operating temperature.
4. Contamination control
Contaminated or ageing fluid accounts for a large proportion of hydraulic failures – between 75% and 95%, depending on who you ask. Any troubleshooting procedure should, therefore, prioritise contamination control before any other remedial action is attempted. In this area, prevention is more effective than cure. A strategy designed to maintain fluid cleanliness should involve using only vendor-recommended fluids to avoid compatibility issues, sealing your reservoirs and equipment openings to protect against moisture and dust ingress, and regularly replacing and inspecting your filters.
5. Temperature levels
Overheating is a common cause of mechanical faults and efficiency loss in fluid power systems. Deviations from the temperature norm can indicate an underlying issue such as a clogged cooler or excessive friction within your system. Monitoring your fluid temperature and keeping it within the recommended temperature range will help extend the lifespan of your components and maintain consistent performance.
6. Verify control calibration
Issues may arise if your control valves are incorrectly calibrated. A key warning sign of this is erratic performance, so periodically check the calibration of your flow control, pressure, and directional valves to make sure that they align with your system’s operational parameters.
7. Environmental awareness
Environmental factors such as high dust levels, ambient humidity, and high temperatures can increase the risk of failures in hydraulic and other fluid power systems. Those designed to operate in austere environments might require a more rigorous preventative maintenance schedule and the use of more durable components, such as reinforced hydraulic hoses more capable of withstanding abrasion and thermal exposure.
What next?
Get in touch with HydraStar today for advice about the most appropriate preventative maintenance and servicing approach for your fluid power application.
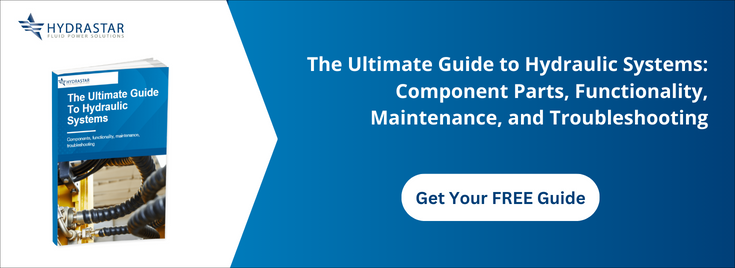