Pilot devices offer an extremely precise way of manually controlling a hydraulic pump and are often chosen instead of computer control kits or automated solutions. Like many components, however, malfunctions may occur, so being able to spot the warning signs early can enable you to take prompt action to prevent serious problems.
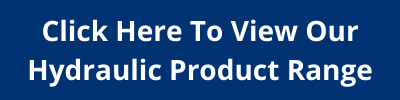
Initially, some warning signs that a hydraulic pump pilot device is faulty may only be subtle. Therefore, it can be difficult to identify emerging problems, so a sudden, complete breakdown is an unfortunate possibility that could lead to an extended period of downtime.
What are the signs that your pilot device is faulty, and is there a preferable alternative?
1) Stuck Buttons
Push button controls are common on some models of hydraulic pump equipment. Frequently, these are spring-loaded to enable easy operation. However, due to wear and tear or an accumulation of grease or other debris, the buttons may become stuck from time to time. When a button is depressed but refuses to rise, a serious jam could occur. Without easy access to the pump, the problem would persist until expert technical support could be obtained.
2) Loose Levers
Pilot devices feature levers and joysticks to offer excellent control for users but, over time, these components can become loose. In this situation, it is difficult to achieve the same level of control. Gears and internal components can suffer wear as a result, such as cracking or shearing. Also, a loose lever may move beyond its natural stopping point (as they are designed to move or rotate only so far). If this occurs, the pump can lose control and serious problems may occur.
3) Stiff Pedals
Some pilot devices have foot controls to support easier stop/start functions. Sometimes the pedals may become stiff or jam completely, making forwards and backwards movements and braking difficult. Repairs may include the replacement of parts; however, if a fluid leak inside the controls has led to extensive corrosion, the cost of repairs may be high.
4) Slow Responses
Ideally, a pilot device should offer real-time results, without delays. Problems with internal computer controls can cause the system to respond less quickly than it should, making it difficult to exert exact control. Identifying the cause of the problem can be tricky, as full pump troubleshooting may be necessary, including digital computer scans and analysis.
Is There a Viable Alternative To Hydraulic Pump Pilot Devices?
Automated solutions are a reliable and cost-effective way to achieve precise control over hydraulic systems. Not only do they eliminate the need for manual intervention, but they offer constant monitoring to ensure that the system is operating optimally. Deviations are promptly reported so that checks can reveal evolving problems. To find out more, get in touch with Hydrastar on 01353 721704.
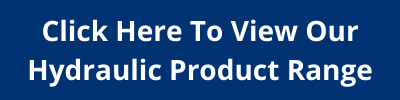