Hydraulic filtration is an essential process for maintaining the health of a hydraulic system by removing contaminants that could affect performance. There are several types of filtration methods that can be used, each with their own benefits and drawbacks. In this article, we discuss four common hydraulic filtration methods: pressure filtration, return filtration, off-line filtration, and inlet (suction) filters.
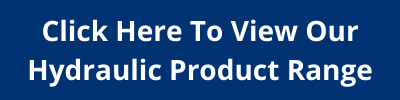
1. Pressure Filtration
Pressure filtration uses a hydraulic filter that is installed downstream from a pump or other component in order to prevent contamination from entering the system. Pressure filtration protects the hydraulic pump, valves, and cylinders from ingress from both solid particulates and liquid contaminants – such as water or oil mist. The process works by creating a barrier of paper mesh or synthetic fibres between the hydraulic system and any external contaminants, trapping them before they enter the system. Pressure filters are designed to withstand high operating pressures and flow rates, making them ideal for applications that deal with large volumes of fluid movement.
2. Return Filtration
Return filtration works in a similar way to pressure filtration but the filters are located on the return line instead of being downstream from the pump. Return filtration is necessary in all hydraulic systems, as it prevents contaminants from re-circulating and possibly damaging the system.
Return filters do not require much maintenance, since they do not have to withstand high pressures or flows like pressure filters do. However, a drawback of return filtration is that it does not protect against all types of contamination, because some liquids can pass through it without being filtered out. Also, if too much particulate accumulates in the filter element it can create backpressure – risking damage to pumps and valves.
To ensure maximum protection against harmful debris without putting extra stress on your hydraulic system, it is important to select the appropriate return filter element with an optimal balance of efficiency and differential pressure.
3. Off-Line Filtration
Off-line filtration involves installing a separate filter unit away from the main system components, which performs its own filtering operations independently of the rest of the system. Off-line filtration enables continuous operation while still filtering out contaminants that could damage your equipment if left unchecked. Off-line filters typically require more maintenance than pressure or return filters due to the need for regular cleaning cycles, but they offer increased protection against particulate contamination sources – making them ideal for sensitive systems where cleanliness is paramount.
4. Inlet (Suction) Filters
Inlet filters are installed upstream from a pump to capture dirt particles suspended in oil and prevent them from entering the system. Inlet filters aren’t universally used or recommended because in some cases they can reduce pump life by increasing the vibrations caused by cavitation inside the pump housing, due to changes in air pressure caused by flow restriction through the filter element.
Selecting The Right Filtration Strategy For Your Application
When determining which type of hydraulic filter will work best for your application there are several factors that need to be considered, including cost-effectiveness, ease of maintenance, the level of protection desired, and how often you anticipate replacing or cleaning your filter elements. For support in making the best choice for your application, please get in touch with one of our hydraulic specialists today on 01353 721704.
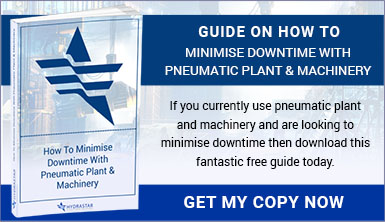