Reliable hydraulic hoses are the unsung heroes of many industrial operations. By focusing on routine visual inspections, professional installation, correct storage, and proactive replacements, operators can significantly reduce their downtime and minimise safety risks. Let’s take a closer look at these proactive best practices for safety and longevity:
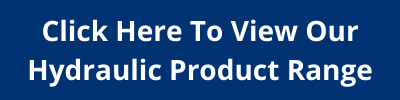
Routine Visual Inspections
Many of the commonest faults with hydraulic hoses can be spotted through simple visual checks. For example, signs of surface degradation caused by cuts, cracks, and abrasions can be easily diagnosed, as are bulges on the outer layer of the material. Inspecting the fitting connections can also diagnose fluid leaks and seepage, and allow rapid resolution of the issue often by simply tightening the connection. Above this, structural concerns can sometimes be identified by testing the flexibility of the hose. Stiffness or kinks in the hose, or simply a reduced level of flexibility, could indicate internal degradation or damage. Metal couplings and connectors should also be inspected for rust and pitting. When to carry out these inspections? Little and often works best. Many operators find that short visual checks at the end of each shift suffice for regularly used applications, while lighter duty systems may only need weekly or monthly checks.
Professional Installation
Time spent on professional installation is time invested in the longevity and safety of your hydraulic system. Simply put, correctly installing hydraulic hoses can reduce unnecessary strain over time, and minimise the risk of premature failure. ‘Professional installation’ involves following the manufacturer guidelines when routing your hoses, making sure that the hose adheres to the specified bend radii. This can vary from application to application. Avoid twisting and stretching when installing a hydraulic hose if possible, as this can weaken the internal structure. And finally, it’s important to avoid any contact with sharp or abrasive surfaces – use protective sleeves or clamps when in doubt.
Storing Spare Hydraulic Hoses
Good hydraulic hose management practices start at the warehouse. Storing your spare hoses properly while awaiting use can prevent premature failure and degradation. The most important factor at play is to store your hoses in a dry and cool environment away from direct sunlight and high temperatures, because UV exposure and excessive heat can weaken the rubber and polymers used in many hydraulic hoses. Hoses can also be damaged by being flattened by heavy equipment, boxes, and materials being stacked on top of them. It’s also worth storing your hoses away from electric motors and other ozone-producing machinery, as this can damage the integrity of some rubber compounds.
Replace Your Hoses Proactively
It’s always easier to replace your hoses proactively at the appropriate intervals than to wait for them to fail. All hydraulic hoses have a finite lifespan, influenced by their working intensity, material, and manufacturer recommendations, and unexpected failure is always a risk no matter how diligent your team are in their visual inspections and maintenance schedule. Following the service life recommendations provided by the hose vendor – even in the absence of visible damage – will help avoid unplanned downtime and damage to your system.
What Next?
For more information about hydraulic hose management and how to extend the longevity and safety of your fluid power applications, please contact one of the experienced team at Hydrastar today by clicking here, or by calling 01353 721704.
Image Source: Canva