In the precision world of manufacturing and engineering, few occurrences hold more of a sting than unexpected downtime. Downtime is often more than merely an inconvenience: for critical fluid power applications, downtime can cause a domino effect that impacts production schedules, overheads, and in serious cases, staff safety.
Proactive maintenance is not a novel concept but is often neglected in practice in favour of reactive repairs. With proactive maintenance, you shut your system down at scheduled intervals to replace worn parts and carry out servicing, in order to reduce the risk and expense of repairs long term. With reactive repairs, you keep your system going until there is a known issue, and then you replace the necessary parts, working to the old adage ‘if it ain’t broke, don’t fix it’.
In this article, we’ll look at how proactive maintenance can often save operators, OEMs, and engineers money and downtime over the costly and inefficient practice of reactive repairs.
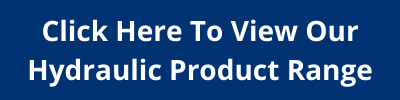
The Unseen Costs Of Reactive Repairs
When a fluid power system malfunctions in some way, the instinct of most engineers is to react immediately. The faulty component is identified and removed, damaged seals are replaced, and the system is re-pressurised. It’s a reactive measure, and one that is carried out as swiftly as possible.
However, there are unseen costs to reactive repairs.
To begin with, reactive repairs can be expensive, frequently requiring you to order a part at short notice and in low volume, which is always costlier than ordering in bulk and in advance. As well as this, one repair often leads to another. The domino analogy plays again here: one failed component can trigger a chain reaction of issues. What starts as a seemingly simple fix can quickly escalate into a costly overhaul of the entire system.
It’s not uncommon for a straightforward repair to be the start of a series of unscheduled shutdowns, amounting to thousands of hours of lost productivity.
Other unseen costs arise from the fact that most reactive repairs are conducted in haste in order to minimise downtime. Unfortunately, hasty repairs can lead to anticipated errors that could increase the risk of future system vulnerabilities and could even compromise the well-being and safety of your workforce.
The Strategic Advantage Of Proactive Maintenance
Imagine a different scenario. A fluid power application has been meticulously maintained, regular checks have identified a potential issue, and pre-emptive repairs have been made. When the system is finally shut down for scheduled servicing, the downtime is minimal: a controlled and scheduled shutdown with minimal impact on your operation. The advantages of such a proactive maintenance approach are as clear as they are compelling.
Cost effectiveness is perhaps the most immediate advantage – by nipping issues in the bud, you’re avoiding the possibility of larger and costlier repairs in the future. Operators and engineers also benefit from the predictability and safety associated with a regularly maintained system, bringing us to the next advantage to your operation: that of reliability.
Proactive and predictive maintenance instils a sense of dependability in your applications. Knowing that the system has been consistently and professionally maintained, with a clear audit trail, lends assurance to operators and production managers alike. This operational calm translates into tangible improvements in efficiency and performance.
Developing Proactive Strategies For Your Fluid Power Systems
Proactive maintenance over reactive repairs is a proven model for operational efficiency and safety management, rooted in reducing risk and enhancing returns. However, implementing proactive maintenance into your fluid power systems begins with a shift of perspective. Maintenance staff need to transition from firefighting mode to a structured ongoing evaluation approach, which requires an investment in training and resources, as well as clear communication about the benefits of proactive maintenance.
Regular systematic inspections should then be conducted, and based on this, a personalised schedule of preventative maintenance should be established. Depending on your application, this could include oil and filter changes, regular pressure and temperature monitoring, and the replacement of worn components before they have the chance to fail.
Next Steps
Unfortunately, is not possible to completely rule out the risk of component failure and unscheduled downtime, but by implementing proactive maintenance, you fortify your applications against unforeseen threats, minimising the cost and inconvenience of repairs.
At Hydrastar, we stock a wide range of reliable and high-performance components for fluid power systems, available at competitive prices. To find out more, and how they can be incorporated into your proactive maintenance schedule, please call one of our team today on 01353 721704.
Image Source: Canva