Contamination while replacing a hydraulic hose is a significant concern, as an ingress of contaminants can impair the performance of your hydraulic system, leading to inefficiency, increased wear and tear, and even potential system failure. Contaminants can enter a hydraulic system in various ways during hose replacement, and are often introduced through the hose ends during cutting or assembly, and they may also enter while the system is open during hose replacement.
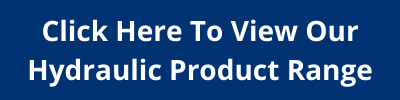
Why You Should Take Contamination Risk Seriously
The risk of contamination is an important one because contaminants can often cause blockages in hydraulic systems, increase friction (and therefore raise the risk of overheating) and damage seals and other key components. This cumulative damage may reduce your system’s lifespan and could also increase your lifetime maintenance costs and the risk of unscheduled downtime. In severe cases, moreover, damage arising from contamination could lead to catastrophic failure of important components, posing a safety risk to operators, bystanders, and other machinery.
So, how do you prevent contamination when replacing hydraulic hosing?
1) Use an environmentally controlled hydraulic hose repair facility: a purpose-built hydraulic hose repair facility will have inbuilt safeguards to reduce the presence of dust and airborne particles, specialist cutting equipment that reduces debris during hose cutting, and clean assembly areas. The workspaces in these areas are often isolated from other production stations, further reducing exposure to contaminants, and will often employ a filtration system to capture particulates that could otherwise contaminate hoses.
2) Thorough cleaning before installation: a simple and effective way of reducing the contamination risk is to clean your hose ends after cutting and before installation. The most efficient way of doing so is using a high velocity steam cleaner, dry air, or vacuum system to remove any particulates created during cutting. A projectile launcher can also be used to put a projectile through your hose, effectively removing any remaining debris.
3) Use clean, dry air: when cleaning hydraulic hoses and other components, it is crucial to use clean and dry air. Moisture can cause corrosion inside of your hoses and fittings, while ‘dirty air’ can introduce unwanted particulates. Air should be filtered and dried before use, and we also recommend the use of oil-free compressors.
4) Use caps and plugs: after cleaning the new hoses and before their installation, insert caps and plugs to seal both ends. This prevents the re-entry of airborne contaminants. The caps and plugs themselves should be meticulously clean and ideally should be used only once to avoid cross contamination!
5) Don’t reuse or mix hydraulic fluid: hydraulic fluids can gradually accumulate contaminants over time, and reusing old fluid can introduce these contaminants back into your system. Mixing different types of hydraulic fluids together can also cause chemical reactions that generate particulates and other contaminants, so it is therefore always recommended to use fresh and clean hydraulic fluid of the correct type whenever you replace your hoses.
6) Don’t leave your hydraulic system open: when replacing hoses, the hydraulic system is opened and made extremely vulnerable as an entry point for contaminants. The system should therefore be closed as quickly as possible after hose replacement. This might involve installing temporary plugs or closing valves to isolate open parts of the system.
Find Out More
By being mindful of the contamination risk and using high quality hydraulic components within a sterile working environment, you can significantly reduce the risk of contamination while replacing hydraulic hoses. To find out more about hydraulic maintenance best practices and how to improve the longevity and performance of your hydraulic systems, please talk to one of our engineers today by calling 01353 721704.
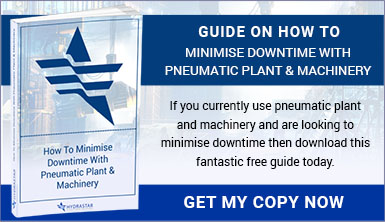