Hydraulic hoses are the blood vessels and arteries of hydraulic systems, transferring the pressurised fluid from one device to another within a system, and conveying the energy required to operate complex machinery and industrial applications. For hydraulic design engineers, therefore, specifying the right type of hydraulic hose is crucial to sustaining the proper functioning of the system and preventing any damage due to incorrect hose selection. In this article, we’ll look at the main commercially available hydraulic hose types, with suggested applications.
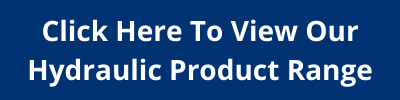
Hydraulic Hoses By Type
- Suction hose: Suction hoses transport fluids from lower pressure areas to higher pressure areas, and feature an internal helix wire that provides the necessary support to the hose. The recommended working pressure for suction hoses is around 150 psi.
- Return line hose: Return line hoses, or hydraulic oil hoses, are used to channel hydraulic fluid back to its reservoir. Most hoses operate at around 100 psi and are best suited for use in low pressure petroleum-based hydraulic fluids.
- Reinforced hose: Reinforced hoses feature an additional reinforced layer to prevent kinking and bursting within high-pressure operating environments. Many reinforced hoses are designed to operate at pressures of 6000 psi or more, and are therefore widely used in construction, mining, and forestry applications, among others.
- Thermoplastic hose: Thermoplastic hoses are flexible and lightweight and are compatible with a wide variety of hydraulic fluids. Working pressures for thermoplastic hoses can be as high as 10,000 psi, making them suitable for high pressure applications such as hydraulic jacks, tools, or lifts.
- Steel braided hose: Steel-braided hoses are robust hoses designed for high pressure applications, with many products delivering a maximum operating psi of 6000 psi. The steel braiding delivers additional strength to the hose, making it more resistant to wear and tear, impact, cuts, and abrasion.
- Flexible low-pressure hose: Flexible low pressure hoses are best suited to lower pressure hydraulic environments, including pneumatic tools, with a working pressure for most products being around 300 psi.
- High pressure hose: By contrast, high-pressure hoses are specifically designed to handle the most demanding hydraulic applications, including earthmoving and construction equipment, heavy duty plant, and industrial machinery. Working pressures are around 6000 psi for most components, with some offering higher maximum operating pressures.
- Four spiral hose: Four spiral hoses have a four layered design, delivering added strength to handle higher pressure hydraulic applications. These hoses are used in mining, construction, and off-road mobile equipment, with working pressures of 6000 psi or more.
- Flange hose: Flange hydraulic hoses are designed to connect hydraulic systems to external components using a flange connection. Working pressures vary widely from 800 psi to 17,000 psi or more, and these hoses are used in an equally diverse range of applications, from offshore drill ships to tankers, marine applications, and heavy construction machinery.
- Metric fitting hose: With an operating pressure range of 500 to 1500 psi, metric fitting hoses are designed to attach with metric-sized fittings and are widely used in mobile hydraulic systems and industrial equipment. These are expensive hoses compared to other components but save time and money on installation due to their easy fit connections.
- Multipurpose hose: Multipurpose hoses are adaptable to a wide range of applications, with the capacity to transport pressurised fluids or gases. Working pressures for these hoses vary from 200 to 1000 psi, so check with your manufacturer before specifying a component in your design. Multipurpose hoses are useful for their versatility, durability, and flexibility, but are not usually suited to high pressure applications.
- Constant pressure hose: Constant pressure hydraulic hoses are designed to handle constant pressure levels throughout a hydraulic system to improve overall performance. Working pressures hover around 3000 psi on average, making them suitable for various industrial and mobile applications.
- Rubber hydraulic hose: Rubber hoses feature a central rubber tube, reinforced with braided wire for added strength. These hoses are widely used in hydraulic design due to their flexibility, reliability, and durability, with operating pressures around 3000 psi.
- Teflon hose: Teflon-coated hydraulic hoses are designed for high temperature and corrosive applications in which traditional rubber hoses do not perform as well. These components feature a Teflon tube with a maximum operating pressure of around 5000 psi. Teflon is also naturally resistant to acids, petroleum products, and many industrial chemicals.
What Next?
As different types of hydraulic hose are designed to suit specific applications, temperature ranges, operating pressures, and working environments, it is essential to select the right type of hydraulic hose to optimise your system performance and efficiency, and to minimise operating risk. For advice specifying the right components for your system, please get in touch with Hydrastar today by clicking here.
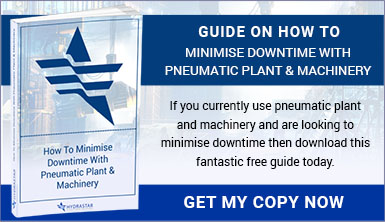