All hydraulic fluid power systems, no matter how diverse, rest on five fundamental operating principles. To develop a versatile and efficient means of transmitting power, therefore, it is essential that any hydraulic system design accommodates these principles within the design, maintenance, and troubleshooting stages.

Principle One: Pascal’s Law
Pascal’s Law or Principle forms the theoretical bedrock of hydraulic power systems, stating that pressure applied to an enclosed fluid is transmitted equally and undiminished to all points within the fluid.
According to this principle, any applied force on a confined fluid (e.g. hydraulic oil within a cylinder) results in a pressure increase that propagates throughout the system. The extent of the force’s distribution relies on the systems size, shape, and overall design. By leveraging Pascal’s law, hydraulic power systems enable engineers to transmit force over large distances and amplify it, yielding precise power control for various applications.
Best practices to ensure efficient pressure transmission:
- Use high-quality hydraulic fluids with the correct viscosity.
- Minimise the risk of leaks and air entrapment in your hydraulic lines.
- Sustain consistent pressure throughout your system.
Principle Two: Continuous Flow Of Fluid
For a hydraulic system to function efficiently, a continuous flow of fluid must be maintained, and the Continuity Equation states that the rate of fluid flow throughout a system remains constant, meaning that the product of the cross-sectional area and flow velocity at any point will be constant. In other words, if the area narrows, the fluid viscosity increases, and vice versa.
Optimal flow is achieved by creating a closed-loop configuration connected to core components such as pumps and valves. Pumps are effectively the systems heart, ensuring that the fluid flows as required to perform the intended work. Valves, meanwhile, enable precise direction and flow control, allowing targeted performance.
Best practices to optimise fluid flow in hydraulic systems include:
- Specify correctly sized and rated hoses, pipes, and valves.
- Avoid sharp bends and unnecessary changes in flow direction.
- Monitor and control flow rates across the system to avoid cavitation.
Principle Three: Pressure And Flow Control
Pressure and flow control, or energy balance, are essential elements of hydraulic system design in order to maximise efficiency and safety. The system’s flow and pressure directly impact its ability to maintain the desired speed or force levels on the applied load. Bernoulli’s Principle states that energy is exchanged between a fluid’s kinetic, potential, and pressure energies as it flows through a system.
Pressure and flow are moderated by means of pressure relief valves and flow control valves, which protect the system for excessive pressure, and regulate the hydraulic fluids velocity to ensure stable and controlled motion.
Best practices to maintain energy balance in a hydraulic system:
- Optimise pump and motor selection to match the power requirements of your application.
- Use correctly sized and configured accumulators to store energy.
- Incorporate energy recovery techniques like regenerative circuits.
Principle Four: Fluid Selection And Maintenance
Selecting the right fluid is imperative for efficient power transmission and system performance. For overall system effectiveness, the fluids chosen must possess the appropriate level of viscosity, optimum temperature performance, and resistance to chemical degradation and wear. Regular fluid maintenance and replacement is essential to ensure reliable hydraulic operations – this may involve periodic oil changes, fluid analysis, and filtration procedures to minimise the risk of contamination.
Best practices include:
- Choose a fluid type compatible with your system materials and that is optimised for the specific application and operating conditions.
- Implement a fluid testing and monitoring schedule to keep contamination levels within your application’s acceptable limits.
Principle Five: Heat Dissipation And Management
Closed hydraulic systems are designed to minimise heat dissipation and conserve energy, but nevertheless, stringent temperature management is vital to sustain the longevity and performance of any hydraulic system. Excessive temperatures can deteriorate fluid quality, degrade seals, and increase the risk of leaks, compromising the efficiency of your system.
Heat management best practices in hydraulic systems include the use of heat exchangers, cooling fans, and radiators – engineers must design systems capable of maintaining the optimal temperature levels and ensure that adequate heat dissipation measures are in place to avoid overheating.
Next Steps
At Hydrastar, we work with some of the world’s leading fluid power manufacturers to provide a wide range of hydraulic components for a variety of commercial and industrial applications. For more information, please contact one of our experienced engineers today by calling
01353 721704. We can help you with fluid selection, system design, component selection, safety and maintenance, and system management to develop smooth running and long-lasting hydraulic applications.
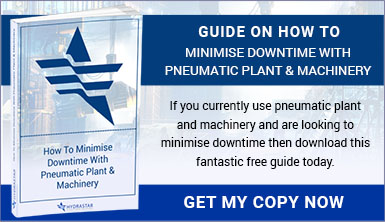