Compression fittings are the nuts and bolts, quite literally, of hydraulic engineering: essential components that connect tubes or hoses to various components, such as valves, pumps, and actuators, in a hydraulic assembly. Their compression action forms a tight seal, which prevents leaks and preserves the integrity of the hydraulic fluid transmission.
In this article, we’ll look at the main differences between two core types of compression fittings – single ferrule and double ferrule, exploring the different applications and identifying the better fit for your specific hydraulic system requirements.
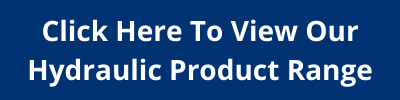
Single Ferrule Hydraulic Compression Fittings
Single ferrule compression fittings, sometimes known as ‘bite type’ fittings, are made up of three parts – the nut, the body, and the ferrule. Their construction includes a single compression ring that bites into the tube or hose when assembled, creating a secure and leakproof joint.
Applications: single ferrule compression fittings are commonly used in medium duty hydraulic applications, and in industries where ease-of-use and compact design are essential considerations, such as automotive manufacturing.
Pros: single ferrule fittings are easy to assemble and disassemble, and require fewer components than their double ferrule counterparts.
Cons: the fittings are more vulnerable to system vibrations and the associated concern of joint loosening over time.
Double Ferrule Hydraulic Compression Fittings
The main difference between a double and single ferrule compression fitting is that doubles have an additional ‘anchoring’ or ‘key’ ferrule alongside the primary compression ferrule. This two-ferrule system helps evenly distribute forces across the fitting, providing a more robust connection that can handle higher pressures without risking leaks.
Applications: double ferrule fittings are often the go-to choice for heavier duty and high pressure applications, where reliability under extreme conditions is critical – such as industrial and petrochemical applications.
Pros: while double ferrule fittings can be more complex and take longer to assemble than singles, they provide superior resistance to system pressure and vibration. They are also known for their ability to effectively seal against hard plastic and metal tubing, which can be a challenge for single ferrule fittings.
Cons: double ferrule fittings have a higher price point and take more time and skill to assemble and disassemble.
Will That Be A Double Or A Single?
The choice between a single and double ferrule fitting is not as simple as choosing between a double or single scoop of ice cream: The decision should be based on the operational parameters of your system, as well as the level of reliability and precision you need. As a rule of thumb, single fittings are usually sufficient for moderate pressure demands with their straightforward design, while double fittings are the standard for high intensity applications and challenging operational environments.
Consider The Following Before Selecting Your Components:
- Carefully assess your system requirements, including the expected operating pressure and temperature range.
- Check the compatibility between the fitting material and your hydraulic fluid.
- Consider the tubing/hose material and its tolerance to vibration and movement.
Find Out More
At Hydrastar, we stock a wide range of high-quality components for fluid power applications. To find out more, please browse our product selection, or contact one of our experienced team directly if you have any questions.
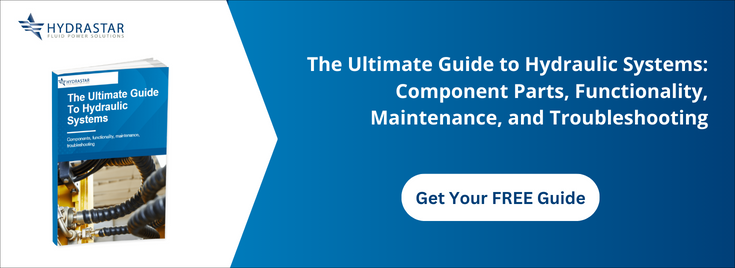