Fluid dynamics is the beating heart of some of the world’s most powerful and important machinery, spanning sectors as diverse as agriculture to construction, to renewable power generation. The ability to engineer an efficient hydraulic system is not just an art form, but a critical step towards greater energy conservation and higher performance, helping ensure that every joule of energy is harnessed to its maximum potential.
In this article, we’ll look at four ways of building efficiency optimisation into a hydraulic system at the design stage.
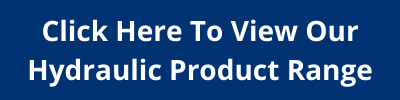
1. Core Design For High-Performance Hydraulics
A hydraulic system only performs as well as its constituent components, so efficiency optimisation begins with selecting the best components for both performance and energy use. To achieve your efficiency goals, a structured approach to design is essential, beginning with your selection of core components:
- Hydraulic pumps and motors: your choice of pump and motor technology can directly impact your system’s efficiency. Axial piston pumps and motors, for example, are known for their high efficiency rates due to their ability to withstand high pressures and speeds, making them a good choice for many industrial applications. Variable displacement pumps and motors, especially components with electronic controls, also increase efficiency by allowing on demand operation, minimising unnecessary energy use.
- Hydraulic cylinders: hydraulic cylinder performance often dictates the overall efficiency of your motion control applications. The newest generation of hydraulic cylinders is engineered for reduced friction, improved sealing techniques, and with advanced materials that counteract wear and extend life cycles, all of which contribute to lifetime energy savings.
- Smart components: the growth of the Internet of Things has strong implications for hydraulic efficiency. Smart and interconnected hydraulic components have the potential to gather vital operational data that can be used to react to system efficiencies instantly, leading to improved energy use and performance over time.
2. Smart Tubing And Fittings Strategies
The tubing and fittings used in a hydraulic system can have a critical impact on the system’s overall efficiency. For example, specifying the optimal tube size and material for your application can reduce pressure drop, which is a common source of energy loss in hydraulic systems. Correctly sized and smooth walled, corrosion-resistant tubing not only assists efficient energy transfer but also simplifies system maintenance for your engineers, and reduces the risk of faults.
And in terms of fittings, specifying high quality fittings and ensuring precision and accuracy during installation can drastically reduce the number of leaks experienced by your system. A streamlined and leak free system is better able to maintain the necessary pressure to operate the application efficiently.
3. System Design And Optimisation
Fluid power engineers now have a wide range of simulation and analysis tools at their fingertips, to help them meticulously design each system to deliver the highest levels of performance. Flow simulation software, for instance, can help optimise a hydraulic system by predicting fluid behaviour under various conditions, identify areas of turbulence, and suggest design modifications that can enhance performance and minimise energy waste. Many hydraulic applications can also be fitted with adaptive control systems that react to changing operating conditions. These systems can adjust flow rates, pressure, system loading, and other parameters immediately or at short notice in response to sensory data, in order to maintain efficient operation.
4. Maintaining Efficiency In The Real World
Designing an efficient system ‘on paper’ and sustaining this efficiency while at the coal face is an ongoing challenge that requires a commitment to both monitoring and adjustments. This is why control systems play such a crucial part in modern hydraulic design. The control system is like the brain of the fluid power systems, and as such, must be carefully maintained. Regular software updates and hardware checks help keep your system working optimally, ensuring that energy isn’t wasted due to outdated controls. By fine tuning your control systems and software programs to match the specific efficiency requirements of your application, long term energy costs can be saved without sacrificing performance.
Next Steps
To find out more about efficient hydraulic design and the best choice of components to help you achieve your project goals, please contact one of our experienced fluid power engineers today by 01353 721704.
Image Source: Canva