Recent innovations in the fluid power sector have led to significant improvements in pneumatic system design, efficiency, and safety, with technological features such as smart pneumatics and variable speed drive compressors changing the design landscape for many industrial applications. So, what are the key considerations to bear in mind now when designing a pneumatic system?
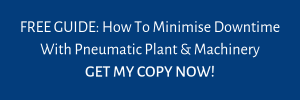
Air Flow Rate And System Pressure
Despite the many factors that have changed, the primary concern in designing a pneumatic system remains the calculation of your required airflow rate and system pressure. In general, the performance of a pneumatic system is directly related to its capacity to maintain a consistent and adequate flow of air and stable pressure levels, so to ensure optimal performance, it is necessary to:
- Determine the pressure and flow rate required for each component within your system.
- Consider the effect of pipe lengths and bends on airflow – these factors can considerably influence pressure drops and flow rates.
- Specify the right size of compressor, valve, and other system components to meet the demands of the application and account for any pressure losses that may occur throughout the system so that performance is not compromised.
Leakage Control And Prevention
Air or fluid leakage is the most common issue encountered in pneumatic systems, leading to a loss of efficiency and increased energy consumption. To minimise the risk of leaks at the design stage, it is crucial to:
- Specify the appropriate tubing, fittings, and connectors to create a secure seal that can withstand operating pressures.
- Implement a regular preventative maintenance schedule and visual inspections to detect and repair leaks at the earliest stage.
- Utilise pressure regulators to maintain the optimal pressure level within your system, preventing excessive pressure conditions that may exacerbate existing leaks.
Operational Safety Mechanisms
Safety is of the utmost importance when designing a pneumatic system, and to ensure the safety of operators and equipment, design engineers should consider:
- Installing pressure relief valves to prevent over-pressurisation, which can lead to critical system failure or damage.
- Incorporating a lockout or tag out procedure for isolating energy sources and securing equipment during maintenance and/or troubleshooting.
- Implementing redundancy in critical system components, e.g. backup compressors or additional control devices, to mitigate the risk of equipment failure.
Smart Technology And The Internet of Things (IoT)
While the function of fluid power systems remains largely unchanged by new technologies, smart integrations have opened new possibilities for energy conservation, monitoring, and automation that can increase both the safety and performance of pneumatic applications. Interesting examples of the intersection of ‘industry 4.0’ technology with pneumatic engineering include:
- Smart pneumatics: The integration of digital sensors, monitoring devices, and data analytics allows engineers to optimise system performance in real time, identify issues before they become critical, and lower the lifetime cost of maintenance. In automotive assembly plants, for example, IOT-enabled pneumatic systems allow real-time monitoring and remote adjustments to system parameters without direct human intervention, allowing operators to adjust operations according to production needs, and reduce energy consumption.
- Energy-efficient compressors: the development of variable speed drive (VSD) compressors, which automatically adjust the motor speed to match the demand for compressed air, lowers energy consumption needs and operating costs in a wide range of pneumatic systems.
What Next?
At Hydrastar, we supply advanced pneumatic cylinders, mountings, sensors, and valves from Festo and other leading industry suppliers. For advice choosing the right components for your application, please call one of our engineering specialists today on 01353 721704.
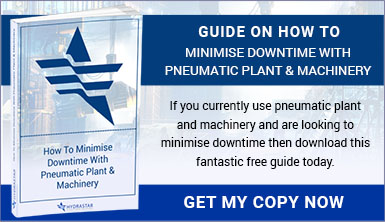